Walk-In Freezer Repair: A Complete Guide for Businesses
- Dec 7, 2024
- 4 min read
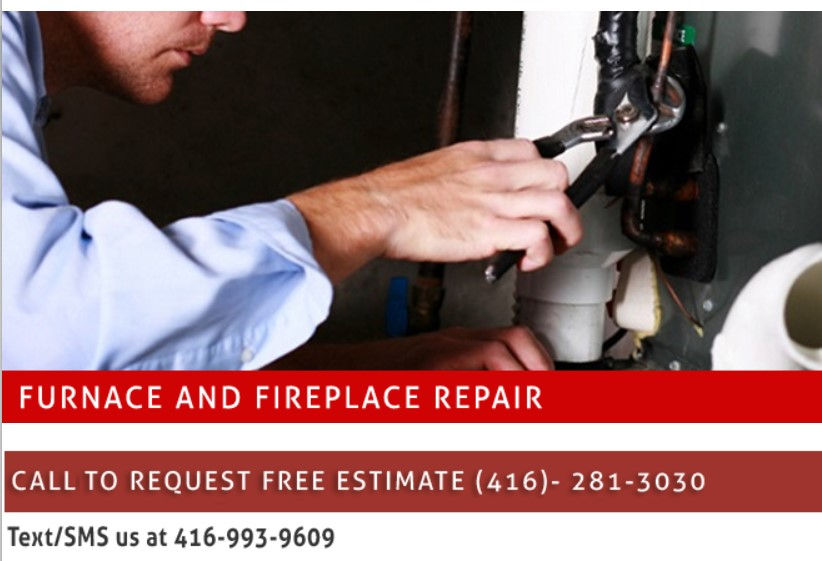
Walk-in freezers are an essential part of many businesses, from restaurants to grocery stores and warehouses. These units provide critical refrigeration to preserve perishable goods, but like all equipment, they require regular maintenance and occasional repair. When something goes wrong with a walk-in freezer, it can lead to significant losses, making timely repairs crucial.
1. Common Issues in Walk-In Freezers
Understanding the common issues that affect walk-in freezers can help identify problems early and prevent major breakdowns. Here are some of the most frequent problems:
a. Freezer Not Cooling
If your walk-in freezer isn't cooling properly, it can result in spoiled inventory. Common causes include:
Thermostat malfunction: A faulty thermostat can prevent the freezer from maintaining the right temperature.
Dirty condenser coils: Dust and dirt buildup on condenser coils can cause the compressor to overheat and fail.
Refrigerant leak: A loss of refrigerant can lead to insufficient cooling. Leaks in the evaporator or condenser coils are common culprits.
b. Strange Noises
If your freezer is making unusual sounds, it could indicate a mechanical issue:
Compressor noise: A malfunctioning compressor can make loud, irregular noises, signaling an internal issue.
Fan problems: A noisy fan could indicate an obstruction or a malfunction in the evaporator or condenser fan.
c. Ice Build-up
Excessive ice buildup on the evaporator coils can cause temperature fluctuations and decreased efficiency. This might be caused by:
Defrost timer failure: The defrost system helps prevent ice accumulation. If it fails, ice can build up quickly.
Door seal issues: If the door seals are damaged, warm air can enter the freezer, causing frost buildup.
d. Frequent Cycling
If the freezer is cycling on and off more frequently than usual, it could mean the system is working harder than it should:
Dirty condenser coils: As mentioned earlier, dirty coils can cause the system to overheat and cycle excessively.
Improper airflow: Lack of airflow due to blocked vents or a malfunctioning fan can stress the system.
e. Power Issues
A sudden loss of power to the freezer can be caused by:
Electrical problems: Issues with the freezer’s power supply, fuses, or wiring can cause it to stop working.
Faulty thermostat or control board: A malfunctioning control board or thermostat can fail to send the necessary signals to the freezer’s motor.
2. When to Call a Professional Technician
While some basic issues can be fixed by cleaning or adjusting the freezer, others require a professional technician. Here’s when to call in an expert:
Refrigerant leaks: Only certified technicians can handle refrigerant leaks due to environmental laws and safety concerns.
Compressor failure: Replacing or repairing a compressor requires specialized knowledge and equipment.
Complex electrical issues: If the problem lies with the freezer's electrical system, it’s best to hire a licensed technician.
System-wide breakdowns: For problems involving multiple components, like the defrost system or control board, a professional should handle the diagnosis and repair.
3. Preventive Maintenance Tips
Preventive maintenance is key to extending the life of your walk-in freezer and minimizing downtime. Here are some tips:
a. Regular Cleaning
Condenser Coils: Clean the condenser coils every 3-6 months, depending on the amount of dirt and dust they accumulate. Dirty coils reduce the efficiency of the system and can lead to premature failure.
Evaporator Coils: Clean the evaporator coils to prevent ice buildup and maintain airflow.
Fans: Check and clean the fans to prevent them from becoming clogged with dirt or debris.
b. Check Door Seals
Inspect the door seals regularly to ensure they are not cracked or damaged. Leaky seals allow warm air to enter, leading to temperature fluctuations and higher energy consumption.
c. Monitor Temperature
Regularly check the temperature inside the freezer. If it fluctuates or rises above the ideal range, investigate the cause. Keeping the unit at the correct temperature is essential for food safety and energy efficiency.
d. Defrosting
Make sure the defrost system is functioning properly to prevent ice from building up on the evaporator coils. Regular defrosting can help avoid excess frost and reduce the strain on the compressor.
4. Choosing a Walk-In Freezer Repair Technician
Selecting the right technician is essential for ensuring the longevity of your walk-in freezer. Consider the following when choosing a professional:
Certification: Look for technicians who are certified and experienced in commercial refrigeration.
Experience: Choose a technician who has experience with walk-in freezers specifically.
Reviews and Recommendations: Check customer reviews or ask for recommendations from other business owners in your industry.
Response Time: Fast response times are crucial when it comes to freezer repair, especially if you’re dealing with perishable goods.
Conclusion
Regular maintenance and timely repair of walk-in freezers are crucial for businesses that rely on them. By understanding common issues, performing preventive maintenance, and knowing when to call a professional, you can keep your freezer in optimal working condition. Regular check-ups will not only reduce repair costs but also improve the efficiency of your freezer, ensuring it keeps your products safe and your business running smoothly.
Call To Request Free Estimate: (416)-281-3030 or allcitiappliances@hotmail.com.
Comments